Fenntarthatósági szempontból is jelentős innovációkat tartalmaz a Paksot és Kalocsát összekötő Tomori Pál Duna-híd
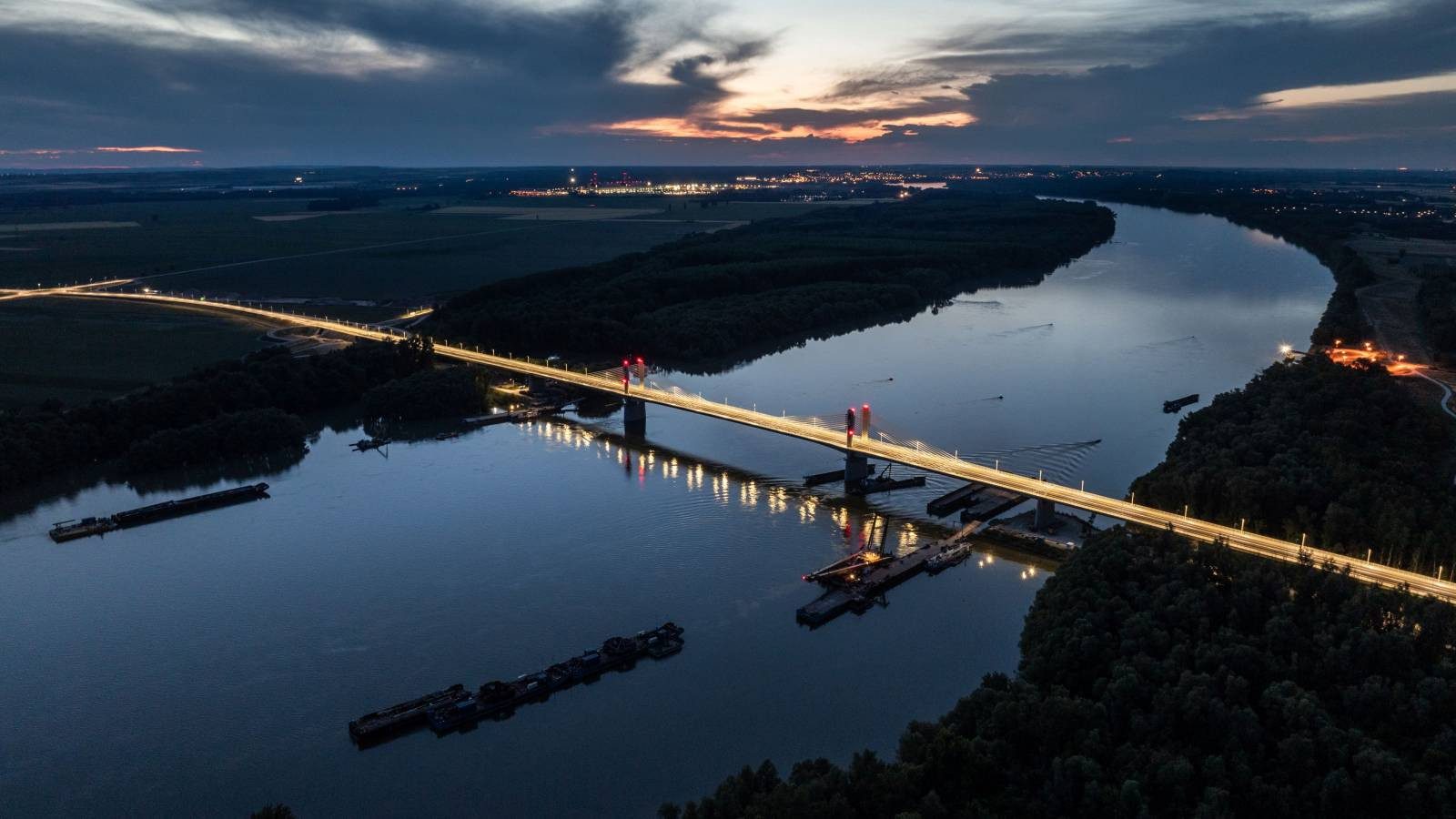
The Tomori Pal Danube bridge linking Paks and Kalocsa also includes significant innovations from a sustainability point of view
Rudolf Kiss, Chief Bridge Engineer, CÉH Zrt.
Modern technology supports green solutions in the design and construction phase
The latest bridge over the Danube, the Tomori Pál Bridge between Kalocsa and Paks, is due to be inaugurated in the first week of June. The launching ceremony of the bridge took place on 14 March: according to an old tradition, the builders celebrate the completion of a bridge with a ceremony of launching the barrel. The tradition is based on an old superstition that the bridge builders made a deal with the devil to build the bridge, but in return the devil demanded the soul of the first person to cross. To break the curse, a barrel is rolled over the bridge. Once the barrel has been rolled, all that remains is to 'dress' the bridge, such as building the asphalt surfacing, installing the railings and lighting - and, of course, the test load.
The work of CÉH zRt. includes the design of the award-winning Megyeri Bridge: "Designing a bridge over the Danube is the pinnacle of the profession for Hungarian designers, requiring the coordinated work of nearly 20 bridge designers," says Rudolf Kiss, chief engineer of the bridge section at CÉH zRt. "The bridge, which consists of three units - the left bank floodplain bridge, the embankment bridge and the right bank floodplain bridge - is 946 metres long in total, 23.26 metres at its widest point," adds Rudolf.
CÉH zRt. also prepared the technological and structural plans for the construction. Special attention was paid to sustainability and the environment during the design and construction of the bridge, as the road leading to the bridge crosses a Natura 2000 site, so conservation issues had to be taken into account. "The EIA was also an opportunity to inform the public, as the different possible routes were discussed with the local communities. - explains the Chief Engineer.
In addition to the designation of the route, the construction technology chosen will also determine the impact the bridge will have on its surroundings - during construction, operation and maintenance. "After studying several different bridge designs, we chose the extradosed type," says Rudolf Kiss, Chief Engineer. "One of the big advantages of this type is that we can achieve larger spans than bridges with a conventional structure, using less material. In addition, we used steel trapezoidal plates instead of reinforced concrete spans, and this type of superstructure, known as a mule, has a lower dead weight, requires less material for the auxiliary structures and less material for the substructures. By reducing the amount of material needed for construction, we have also successfully minimised the environmental impact," Rudolf added.
Our bridge design team has been working together for many years, so we know each other well. József Fodor, CÉH zRt.'s technical designer, played a key role in the team's work to develop the construction technology and how exactly the bridge would be built. Sadly, József Fodor did not live to see the bridge completed - but his colleagues and the bridge-building profession will always associate his name with the bridge.
The bridge and the floodplain bridges are of different construction: the extradosed type bridge is a mule structure (reinforced concrete and steel) designed using 3D software. The software was used to model the steel structures of the bridge to the nearest millimetre, and these models were used as the basis for the production drawings. The structural elements were built in an environmentally friendly production environment and the main girders, assembled from the finished units, were transported to the installation site by water. The technology, transport and organisation used minimised the impact on the Natura 2000 site.
Trial loading of the bridges was successfully completed in early May. At maximum deflection, 20 lorries weighing 40 tonnes were positioned at predetermined points on the bridge. The deflection of the bridge measured at mid-span was 20cm, confirming the rigidity of our static calculations.
During the design process, it was possible to increase the spans of the floodplain bridges, reducing the number of supports and the environmental impact compared to the original design.
"Thanks to modern technology and careful design, the new Danube bridge has been built with structures and materials that ensure a long service life - with low maintenance and repair costs over its lifetime - and that the general work required for the life of any bridge has the lowest possible impact on the environment," says Rudolf Kiss. "Nowadays, the operation of bridges is already monitored by a serious monitoring system - including icing, displacement of the spans, body temperature of the structure - and if intervention is required, the system signals it immediately," he added.
"I am pleased to say that the Paul Tomori Bridge represents a new generation of bridge design and construction, not only with its innovative technology, but also with its environmental considerations". - summarises Rudolf Kiss, Chief Engineer of the Bridge Section of CÉH zRt.
Photos of the bridge by Tamás Dernovics, magyarepitok.hu.